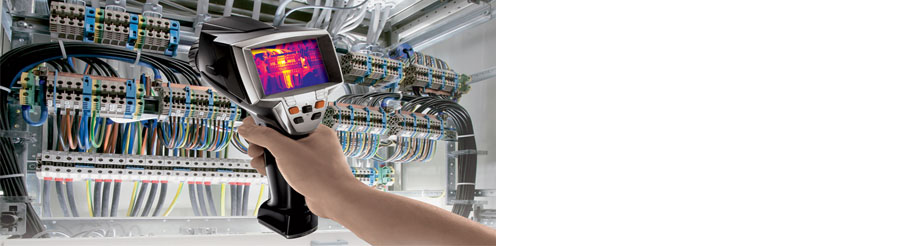
Thermography
Thermography is a method of inspecting electrical and mechanical equipment by obtaining heat distribution pictures. This inspection method is based on the fact that most components in a system show an increase in temperature when malfunctioning. The increase in temperature in an electrical circuit could be due to loose connections or a worn bearing in the case of mechanical equipment. By observing the heat patterns in operational system components, faults can be located and their seriousness evaluated.
The inspection tool used by Thermographers is the Thermal Imager. These are sophisticated devices which measure the natural emissions of infrared radiation from a heated object and produce a thermal picture. Modern Thermal Imagers are portable with easily operated controls. As physical contact with the system is not required, inspections can be made under full operational conditions resulting in no loss of production or downtime.
When carrying out Thermographic inspections, faults are often identified by comparing heat patterns in similar components operating under similar loads. This is an alternative to very precisely predicting the emissivity of each individual component and obtaining absolute temperature values.
Thermal Imagers in Predictive Maintenance Applications
In today’s industrial plants it is essential that unplanned breakdowns and the resultant costly loss of production is kept to an absolute minimum. Predictive maintenance schemes have been introduced to identify potential problems and reduce downtime. Thermography in maintenance applications is based on the fact that most components show an increase in temperature when malfunctioning and faults steadily get worse before failure.
Routine inspection programmers using Thermal Imagers can often offer the following benefits:-
- Inspections can be made under full operational conditions and hence there is no loss of production.
- Equipment life can be extended
- Plant downtime may be reduced
- Plant reliability may be increased
- Plant repairs scheduled for the most convenient time
- Quality of repair work may be inspected
- Electrical Installations
- Mechanical Equipment
- Refractory lined Structures
Inspecting Electrical Installations
Faults in an electrical installation often appear as hot-spots which can be detected by the Thermal Imager. Hot spots are often the result of increased resistance in a circuit, overloading, or insulation failure.
Figure shows a hot-spot created by a bad connection in a power distribution system.
Some of the components commonly inspected are as follows:-
Connectors: When looking at similar current carrying connectors, a poor connection shows a higher temperature due to its increased resistance. Hot-spots can be generated as a result of loose, oxidised, or corroded connectors.